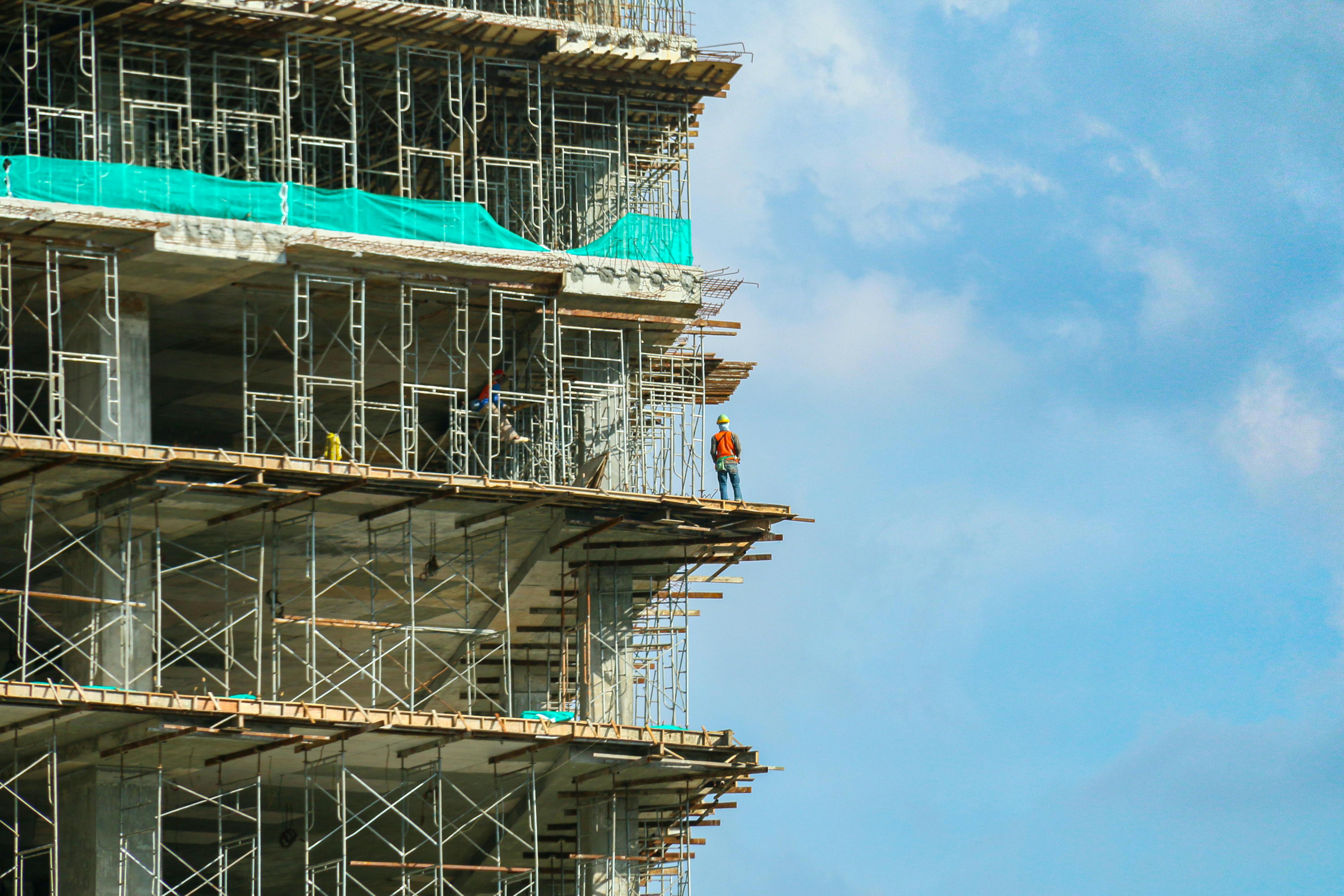
Hot work safety
Working safely while welding, cutting, burning or grinding doesn’t have to bring your business down. Follow these simple tips to stay safe and on budget.
I read in the news lately that an apartment building had burned down due to a fire started by contractors using a torch in the basement. Many people were left without a place to live due to a mistake by a contractor who used a torch to cut through part of the floor. According to the story, there was no fire watch and not even a fire extinguisher on hand during hot work.
Like most safety procedures, the ways to be safe with hot work are simple. You first realize that cutting, welding, or burning metal will produce hot chunks of metal that will go places you may not intend them to go. These hot pieces of metal can set things on fire.
So start by removing anything that can burn from the area. Most permit systems recommend a clearance of 30 feet.
Next, make sure you have a working fire extinguisher and someone to operate it. Don’t depend on the one who cuts, burns or welds to keep an eye out for a fire while you focus on the job.
Both the hot worker and the fire watch should be aware that hot metal pieces can fly, roll, or ricochet a great distance from the work site. They should pay special attention to any cracks or gaps near the workplace. Apparently that’s what happened in the story mentioned above; The sparks entered the wall and ignited the insulation.
Another easily overlooked cause of fires is material on the other side of the wall from where the work is being done. I read about a case where combustible material stacked outside a tank was set on fire while welding inside the tank. Heat can also be transmitted by infrared radiation, as well as by conduction. Therefore, workers must be aware of their surroundings when performing hot work.
There are some places where hot work cannot be done at all. For example, in areas near flammable liquids and vapors, hot work should be avoided. Fabricators will often have to get creative to get the job done without the usual cutting, welding, or burning. Parts may need to be screwed or clamped in place instead of traditional mounting methods.
Flammable and explosive dust is a hazard in some operations. Combustible dust can be very dangerous if ignited in a confined area. I remember the demonstration at the Factory Mutual training center. They spray a cup of flour into a closed cave and ignite it with a spark. The impact of the explosion can be felt across the street from several meters away. Paper and wood dust can easily accumulate on structures and be difficult to extinguish if ignited by hot work.
Again, most safe work practices are easy to implement. But workers can often be driven to cut corners to speed up a job. Supervisors should pay special attention to jobs that start near the end of a work shift or are done by my contractors working at a bargain price. There may be incentives to rush work. The most easily overlooked part at the end of a job is the waiting period after a fire watch.
Sparks can take a long time to incubate in a fire. A spark that has fallen into a crack or crevice can smolder for a long time before becoming large enough to see. The fire watch must remain on the job continuously for at least 30 minutes after the job has been completed. The job site should be checked periodically for the next four hours to make sure no fires have broken out.
I’ve found that it’s hard to get contractors to work at a bid price to meet a four-hour fire watch. It’s best to assign this task to a security guard or other trusted employee who is paid by the hour to be there.
Contractor safety often begins in the bidding process. Start by choosing contractors with a good safety record and who understand the unique hazards of your facility. Make sure contractors understand the hazards they will be working on before they bid. You don’t want to be in a situation where your ability to profit depends on taking unsafe shortcuts.
When estimating costs for a job that involves hot work, make sure the estimate includes labor hours for a fire watch during and after the hot work. These may seem like unproductive costs to a contractor unfamiliar with safe work practices, but they are necessary for good work practice. Having a fire watch effectively doubles the man hours required for a job.
When using a torch, care must also be taken with compressed gas cylinders. Compressed gas cylinders have their own unique hazards. Cylinders must be moved with care using proper procedures. If cylinders are to be lifted, they must be properly rigged to reduce the risk of them falling and damaging a cylinder. Cylinders must be properly secured both during storage and during hot work use. In most cases, a suitable cylinder cart will suffice to adequately support the cylinders and transport them safely to the job site.
Electric welders and grinders have hazards normally associated with electricity. Make sure machines have compatible voltage and wiring is in good condition and well insulated. Hot work can easily damage the insulation of welding and grinding equipment, so it should be inspected frequently and properly protected during the hot work process.
When welding, grinding or burning vehicles, there are special risks that apply. Most vehicles will be powered by a flammable fuel. Make sure fuel is completely contained and hot work is done away from fuel tanks and fuel lines. Fuel tank welding is a specialty best left to those brave souls who specialize in the job.
When hot work is done on a vehicle, it is not practical or possible to remove all combustible material such as wiring harnesses, carpets, siding, and upholstery. Great care must be taken to ensure that heat is not transferred through the car body to fuels on the other side of where the work is being done. I’ve read stories of entire cars lost to under-dash fires or burned carpets due to a simple welding repair that ignited material on the other side of the job.
Keep in mind that wiring can be damaged by hot work, even if it doesn’t catch fire. Heat from welding on a roll cage or patch panel can easily cause an electrical short by heating the insulation on wires hidden within body panels.
Cutting, welding and burning are part of any manufacturing process. Just follow some basic safety steps to make sure the job doesn’t do more harm than good.